Test Material Performance
Automated testing procedures using pressure sensors for inline quality assurance testing have been used to verify that materials meet acceptance parameters for performance and manufacturing defects. In Q/A applications, accuracy is a priority, and when measuring complex surfaces it is necessary to have a conformable sensor that can provide repeatable and reliable data.
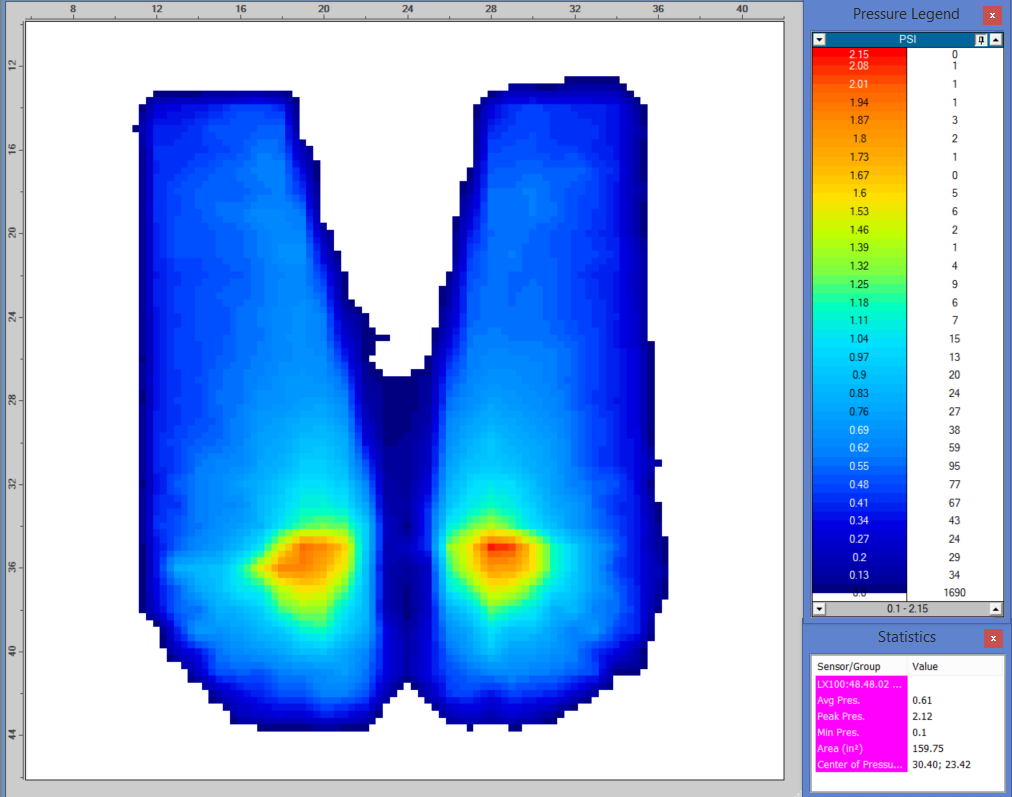
Resolution: 12.7 mm Pressure Range: 0.07-2.7 N/cm2
Our pressure sensors lead the industry in accuracy calibration stability, sensor conformability, and reliability, and are well suited for production line quality assurance testing. Our technology is ideal for manufacturing line testing products for surface pressure performance such as seat construction, foam or gasket material.
Calibration stability ensures accurate data for industrial process monitoring
Due to their calibration stability and accuracy, our pressure sensors provide consistent measurement over thousands of cycles, even under demanding conditions such as those present on production lines. Unlike other pressure sensors, our technology retains its accuracy over long periods of time, which minimizes downtime and maximizes productivity.
Specifications & Performance
The sensors provide consistent measurement with repeated measurement cycles. For industrial process monitoring purposes, calibration stability ensures consistent data over thousands of cycles.
SENSOR | SENSOR SIZE (mm) | SENSING AREA (cm x cm) | CALIBRATION RANGE mmHg (psi) | RESOLUTION |
---|---|---|---|---|
LX100:36.36.02 | 12.70 | 45.0 x 45.0 | 5-200 (0.1-3.87) | Low |
LX100:40.40.02 | 12.70 | 50.8 x 50.8 | 5-200 (0.1-3.87) | Low |
LX100:48.48.02 | 12.70 | 61.0 x 61.0 | 5-200 (0.1-3.87) | Low |
LX100:40.64.02 | 12.70 | 50.8 x 81.3 | 5-200 (0.1-3.87) | Low |
We are an ISO 17025 certified pressure imaging sensor manufacturer
Your ISO 17025 registration requires your suppliers provide verified calibrated test equipment and recalibration processes to maintain your compliance. Unlike other sensors on the market, our sensors maintain their calibration due to the capacitive technology design used and the unique materials used to make these sensors. Our ISO 17025 accreditation means that we have demonstrated competency in producing accurate test and calibration data from our sensors.
Superior Imaging Software
XSENSOR Pro software has been the industry leader for interface pressure testing and measurement for many years. Easy-to-use and very stable, Pro V8 provides specific tools for quality assurance testing. For automated in-line testing test processes our sensors can be used with a DLL.
Sample Application: Automotive Seating
Automotive seating is an example of a complex surface in which bolsters, lumber supports, and seat segmentation are all important factors in the comfort and performance of the seat. Some require thin foam layers over heating, cooling, and mechanical adjust devices, while trying to provide comfort and respond as expected to different suspension designs.
Due to issues with foam consistency, defects, and layering frames underneath and leather on top can result in wide variety from the mean. A sensor which conforms to this unique surface and provides trusted pressure measurements can be set to provide acceptable parameters for the various sections of the car seat.
Applications & Commonly-Used Sensors
Wiper Blades | Go to: Low Pressure Sensors |
Low Pressure Applications | Go to: Low Pressure Sensors |
High Pressure Applications | Go to: High Pressure Sensors |
Seating Applications | Go to: Seating Design |
Tire Applications | Go to: Tire Footprint Testing |